What are the categories of Metal Corrosion?
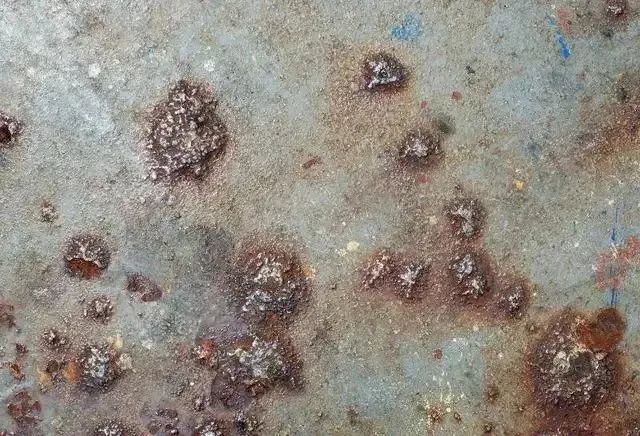
Metal corrosion problems are widespread in many areas of the national economy, such as oil and gas, petrochemical, transportation, machinery manufacturing, etc. It can be said that corrosion problems exist wherever metal materials are used. Metal materials are damaged by the action of surrounding media, which is called metal corrosion.
How many kinds of metal corrosion are there?
Due to the complexity of corrosion phenomenon and mechanism, and the difference of material and environmental factors, i.e. the stress state, the situation and characteristics of metal corrosion vary greatly. Therefore, there are many classification standards and methods, but the common corrosion classification methods are classified according to corrosion mechanism and corrosion form.
According to the corrosion mechanism, it can be divided into chemical corrosion and electrochemical corrosion:
Chemical corrosion refers to metal corrosion caused by direct chemical reaction between metal and non-electrolyte.
Electrochemical corrosion is the damage caused by the electrochemical interaction between metal and electrolyte solution.
According to the corrosion form, it can be divided into two types: comprehensive corrosion and local corrosion:
Overall corrosion occurs on the entire metal surface, which may be uniform or uneven.
Local corrosion is concentrated in some areas of the metal, while other parts have little or slight corrosion. There are many types of local corrosion, which are generally divided into the following types:
Galvanic corrosion: In the electrolyte solution, when dissimilar metals contact, the metal with positive potential will accelerate the corrosion of the metal with negative potential;
Pitting: corrosion damage is mainly concentrated on some active points, and the diameter of the hole is equal to or less than the depth of the hole, which may lead to equipment perforation in serious cases;
Crevice corrosion: corrosion at the crevices of riveting, threaded connection, welded joint, sealing gasket, etc;
Intergranular corrosion: corrosion is carried out along the intergranular, the bonding force between metal atoms is lost, and the mechanical strength of metal is sharply reduced. The metal appearance often has no obvious change before damage;
Stress corrosion: under the combined action of tensile stress and corrosion medium, a kind of cracking failure that occurs and expands at a significant rate; The common types are sulfide stress corrosion cracking and hydrogen sulfide stress corrosion cracking.
Corrosion fatigue: corrosion of metal under the action of corrosive medium and alternating stress.
Corrosion is a costly problem. If the type of corrosion can be quickly identified and the location of corrosion can be found, the potential risk can be greatly reduced. Technicians with professional knowledge can often predict the location where corrosion may occur and select appropriate metal materials in advance to avoid corrosion. This will greatly improve the performance of the production system and improve its integrity and security.