How Does Coiled Tubing Work?
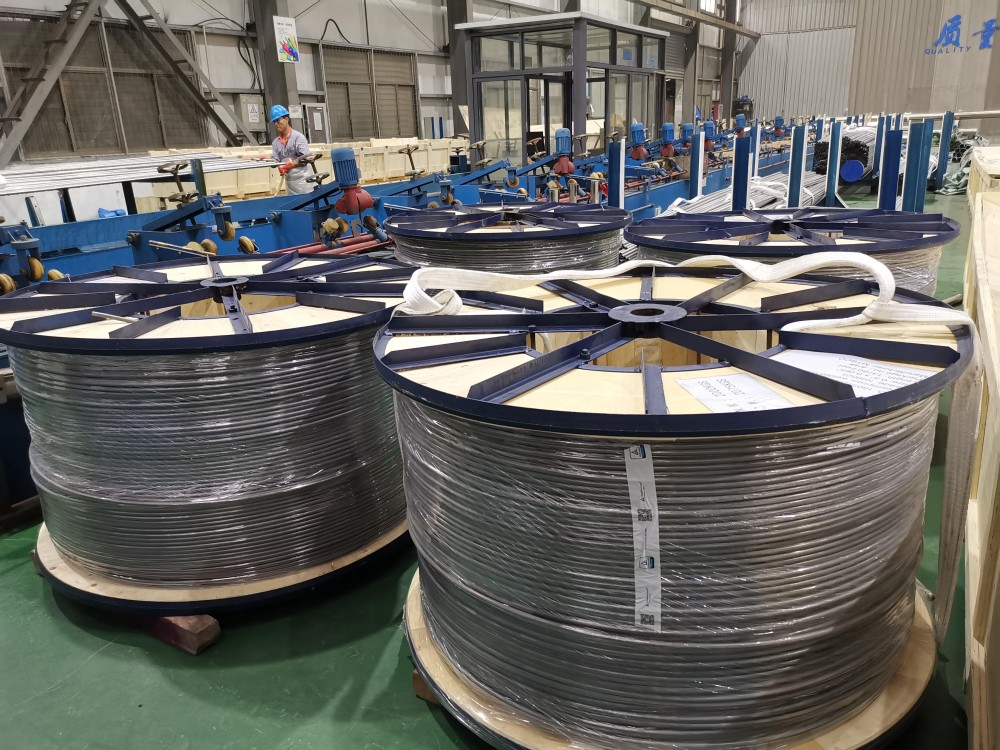
--Key Applications, Benefits, and Operational Best Practices for Oil and Gas and Heat Exchange Systems
Coiled tubing (CT) offers efficient, flexible, and reliable solutions for oil well intervention and heat exchange operations. Learn how coiled tubing enhances fluid transport, corrosion resistance, and high-pressure performance in demanding industrial environments.
Coiled tubing (CT) is a type of tube widely used in the oil extraction and heat exchange equipment industry. CT is wrapped around a drum in a single piece that can reach several kilometers in length, and its elasticity and flexibility enable it to adapt to complex operating environments. It can be directly deployed and used without joints, which significantly improves operational efficiency. The design characteristics of the coil make it have a continuous tube structure without welds, which avoids the leakage problems that may be caused by traditional tube joints. At the same time, its smooth inner wall helps to reduce frictional losses during fluid transport and improve operational efficiency.
Coiled tubing are usually made of stainless steel or nickel alloys, such as 316L, 825, 625, etc., which have significant advantages in corrosion resistance, high pressure resistance, and extreme temperature resistance. Coiled tubing production must meet strict industry standards, such as API 5ST, ASTM A269, and ISO 15156, to ensure its reliability and safety under harsh conditions.
The main applications of coiled tubing include the repair of oil and gas wells, production operations, chemical injection, logging, and fluid transportation in heat exchange equipment. In the oil and gas industry, coiled tubings are commonly used to clear underground obstacles, transport acidizing fluids, and high-pressure operating media. In the field of heat exchange, coils can be used as heat transfer elements to improve heat transfer efficiency and save space.
In practical use, coiled tubings are usually sent into underground or heat exchange systems through specialized equipment. During underground operations, it is necessary to cooperate with coil devices and pressure control equipment to ensure that tubelines enter the wellbore smoothly and operate safely. During the operation, it is necessary to monitor the tension, pressure, and curvature of the tubeline to avoid damage caused by excessive stretching or bending. For applications in heat exchange equipment, it is necessary to ensure good sealing of the interface between the coil and the system, and regularly inspect the surface of the tubeline for pitting or cracks.
There are some key points to note when using coiled tubing. Different work environments have different requirements for the material of coils, for example, nickel based alloys with stronger corrosion resistance should be selected for environments with high hydrogen sulfide content. Before construction, it is necessary to test the seamless, wall thickness, and structural integrity of the tubes, and select the appropriate tube diameter based on the temperature and pressure conditions inside the well. Under high temperature and high pressure conditions, tubelines should avoid prolonged exposure to ultimate stress to extend their service life. In addition, after the homework is completed, the tubeline should be thoroughly cleaned and maintained to prevent residual media from corroding the tubes.
Whether it is processing drilling fluids at extreme high temperatures or conducting efficient heat exchange in severe corrosive environments, coiled tubing provide efficient solutions for the oil drilling and heat exchange equipment industry with their unique material advantages, excellent performance, and flexible applicability. Accurate material selection, scientific usage process, and specialized maintenance are necessary to unleash the maximum potential of the coil and assist customers in successfully and efficiently carrying out their projects