Incoloy 800/800H/800HT Pipe Fittings
Material: Alloy 800H, 800HT, UNSN08810&NO8811; Alloy 800, UNS N08800;
Get Quote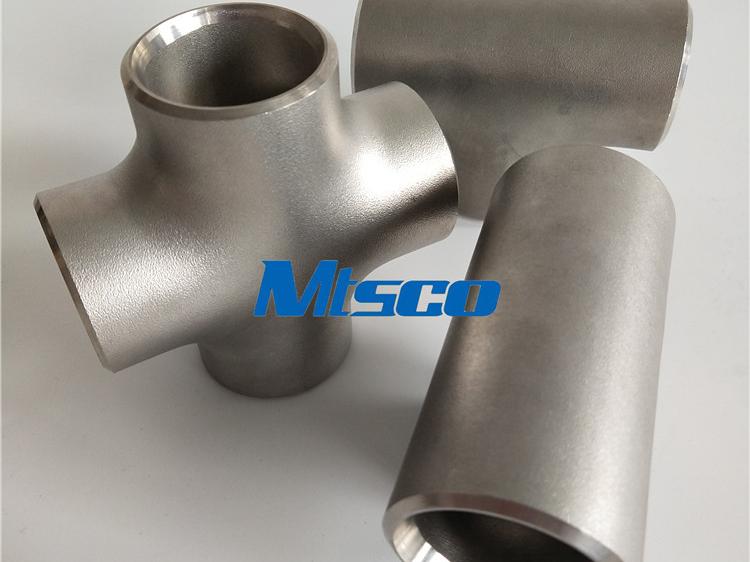
Incoloy 800/800H/800HT Pipe Fittings
Commodity | Concentric Reducer & Eccentric Reducer , Reducing Tee & Equal Tee, Elbow 45° , 90° , 180° , Cross , Cap , etc |
Process Method | Cold Forming |
Grade | Alloy 800/800H/800HT/ 600/601/625/825/C276/C22, TP304/L, TP316/L, S31254, S32205, S32750, ... Austenitic/ Duplex Steel/ Nickel/Cobalt Alloy |
Standards | ASTM A403 , A815, B366, EN 10253-4... |
Size Range | OD: ≤2000mm; ≤DN2000; ≤80'' WT: ≤30.96mm; ≤Sch160 |
Tolerances | according to the specification or customer’s request and drawings |
Applications | oil & gas industry , chemical industry , electric power , boiler and heat exchanger , machinery , metallurgy , sanitary construction etc . |
Advantages of Nickel Alloy 800 For Pipe Fittings:
Strong corrosion resistance: The excellent corrosion resistance of nickel alloy 800 enables its manufactured pipes to be used for a long time in highly corrosive environments, such as the petrochemical industry.
Strong heat resistance: Nickel alloy 800's excellent high-temperature resistance makes it an ideal material for high-temperature pipeline systems, capable of withstanding extreme operating temperature conditions.
Good safety performance: The high strength and excellent corrosion resistance of nickel alloy 800 greatly reduce safety hazards caused by pipe damage or leakage, ensuring the safe and reliable operation of the system.
Widely applicable: This alloy can be widely used in various industrial fields such as oil and gas, chemical, nuclear energy, aerospace, etc., to meet various demanding application requirements.
Long service life: The fittings made of nickel alloy 800 have excellent reliability and durability in high temperature and corrosive environments, greatly reducing the frequency of maintenance and replacement.
Grade | C max | Si max | Mn max | P max | S max | Cr | Ni | Mo | Ti | N max | Cu max | Nb | Al max | Co max | Zr | Fe max | Tu | Va |
Alloy 600/N06600 | 0 | 1 | 1 | - | 0 | 14-17 | ≥72 | - | - | - | 1 | - | - | - | - | 6-10 | - | - |
Alloy 601/N06601 | 0 | 1 | 2 | - | 0 | 21.0-25.0 | 58-63 | - | - | - | 1 | - | 1.0-1.7 | - | - | - | - | - |
Alloy 625/N06625 | 0 | 1 | 1 | 0 | 0 | 20-23 | ≥58 | 8-10 | <0.4 | - | - | 3.15-4.15 | ≤0.4 | - | - | 5.00 remainder | - | - |
Alloy 718/N07718 | 0 | 0 | 0 | 0 | 0 | 17.0-21.0 | 50.0-55.0 | 2.8-3.3 | 0.65-1.15 | 0 | 0 | 4.75-5.5 | 0.2-0.8 | 1 | - | - | - | - |
Alloy 800/N08800 | 0 | 1 | 2 | - | 0 | 19-23 | 30-35 | - | 0.15-0.60 | - | 1 | - | 0.15-0.60 | - | - | ≥39.5 | - | - |
Alloy 800H/N08810 | 0.05-0.10 | 1 | 2 | - | 0 | 19-23 | 30-35 | - | 0.15-0.60 | - | 1 | - | 0.15-0.60 | - | - | ≥39.5 | - | - |
Alloy 825/N08825 | 0 | 1 | 1 | - | 0 | 19.5-23.5 | 38-46 | 2.5-3.5 | 0.6-1.2 | - | 1.5-3 | - | 0 | - | - | ≥22 | - | - |
First, secondary inspection of raw materials
VIP SERVICE
VR (Virtual) Mill Introduction
Professional Remote Technical Guidanceion
Accept Third-party Inspection
Door to Door Shipment
Get QuoteRelated Products: Pipe Fittings: Butt Welded Pipe Fittings
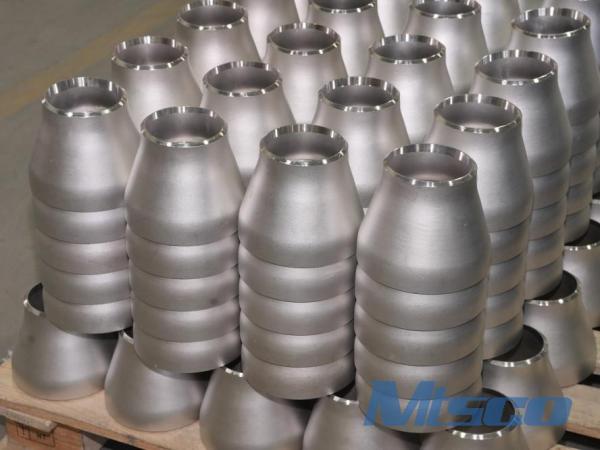
ASTM/ASME A403/SA403 Stainless Steel 310/310S/310H Concentric Reducers
The 310, 310S, and 310H grades offer excellent high - temperature resistance and corrosion resistance, ensuring long - term durability. They are designed to connect pipes of different diameters, providing a smooth and efficient flow of fluids or gases in various industrial applications, such as chem......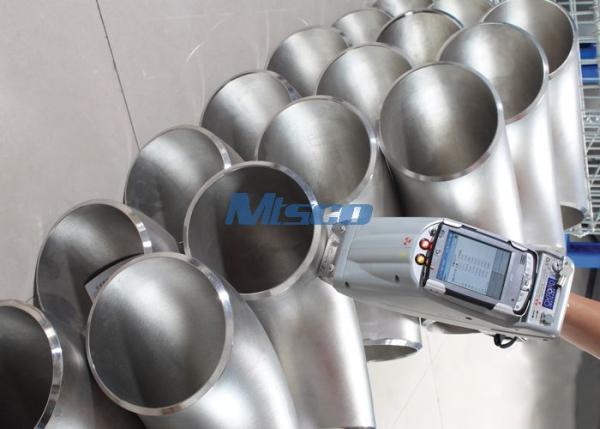
ASTM B366 Alloy B / B-2 / B-3 Nickel Alloy 45 Degree Elbow
MTSCO is a leading manufacturer who is specialized in stainless steel seamless pipes , bright annealed tubes , seamless coiled tubing etc . In order to facilitate customers , we have pipe fittings and flanges too . MTSCO has the most advanced producing and testing equipment . We can totally satisfy ......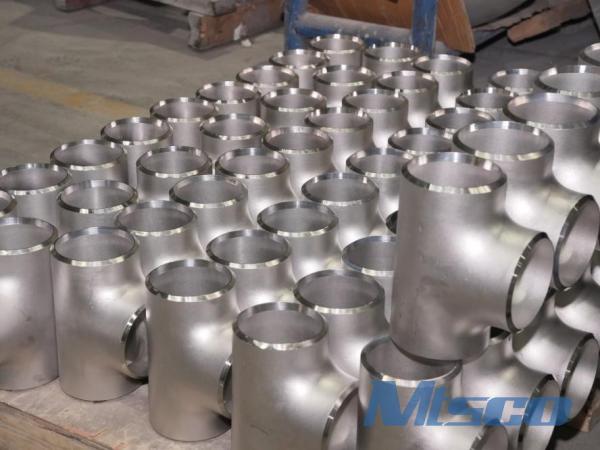
Nickel Alloy 825, UNS N08825, 2.4858, Incoloy 825 Pipe Fittings, Tees, Elbows, Reducers
Nickel Alloy 825 fittings, including tees, elbows, and reducers. This alloy offers excellent corrosion resistance in various environments, such as reducing and oxidizing acids, seawater, and brines. It has good mechanical properties at both high and low temperatures. Whether in chemical processing, ......